In the field of manufacturing and packaging, liquid filling machines play a vital role in ensuring efficient and accurate filling of products into containers. These machines are widely used in various industries such as food and beverages, pharmaceuticals, cosmetics and chemicals. Understanding the principles of a liquid filling machine is vital for anyone involved in production as it has a major impact on the quality and efficiency of the filling process.
Liquid filling machines are used to dispense liquids of a specific volume into containers such as bottles, jars or bags. There are several types of filling machines including gravity fillers, pressure fillers, vacuum fillers and piston fillers, each designed for different types of liquids and containers. The choice of a liquid filling machine depends on a number of factors, including the viscosity of the liquid, the desired filling speed and the accuracy required.
The basic principle of a liquid filling machine is to precisely control the flow of liquid into a container. The process typically involves several key components and steps:
1. Liquid storage
The filling process begins with the reservoir, which stores the liquid to be dispensed. Depending on the design of the machine, the reservoir can be a tank or a hopper. The liquid is usually pumped from the reservoir to the filling nozzle and then dispensed into the container.
2. Filling mechanism
The filling mechanism is the core of the liquid filling machine. It determines how the liquid is dispensed and varies by machine type. Here are some common filling mechanisms:
- Gravity Filling: This method relies on gravity to fill the container. The liquid flows from the reservoir through the nozzle into the container. Gravity filling is suitable for low viscosity liquids and is commonly used in the food and beverage industry.
- Piston Filling: In this method, a piston is used to draw the liquid out of the reservoir and push it into the container. Piston filling machines are suitable for thicker liquids and are highly accurate, making them popular in the pharmaceutical and cosmetic industries.
- Vacuum Filling: This technique utilizes a vacuum to draw the liquid into the container. The container is placed in a chamber that creates a vacuum so that the liquid can be pumped out. Vacuum filling is very effective for foamy or viscous liquids.
- Pressure Filling: Pressure fillers utilize air pressure to push the liquid into the container. This method is often used for carbonated beverages because it helps maintain carbonation levels during the filling process.
3. Nozzle design
The design of the filling nozzle is critical to achieving accurate filling. The design of the nozzle prevents dripping and ensures that the liquid is cleanly filled into the container. Some nozzles are equipped with sensors that detect when the container is full and automatically shut off to prevent overfilling.
4. Control systems
Modern liquid filling machines are equipped with advanced control systems that can accurately measure and adjust the filling process. These systems can be programmed to fill different volumes, adjust filling speeds and monitor the entire operation to ensure consistency and quality control. Many machines are also equipped with touch screens for easy operation and monitoring.
5. Transmission systems
To increase efficiency, liquid filling machines are often integrated with conveyor systems for transporting containers to and from filling stations. This automation reduces manual operations and speeds up the entire production process.
If you have any requirements about liquid filling machine, please check below product.
LQ-LF Single Head Vertical Liquid Filling Machine
Piston fillers are designed to dispense a wide variety of liquid and semi-liquid products. It serves as ideal filling machines for the cosmetic, pharmaceutical, food, pesticide and other industries. They are completely powered by air, which makes them especially suitable for an explosion-resistant or moist production environment. All the components that come in contact with product are made of 304 stainless steel, processed by CNC machines. And the surface roughness of which are ensured to be lower than 0.8. It is these high quality components that help our machines achieve market leadership when compared with other domestic machines of the same type.
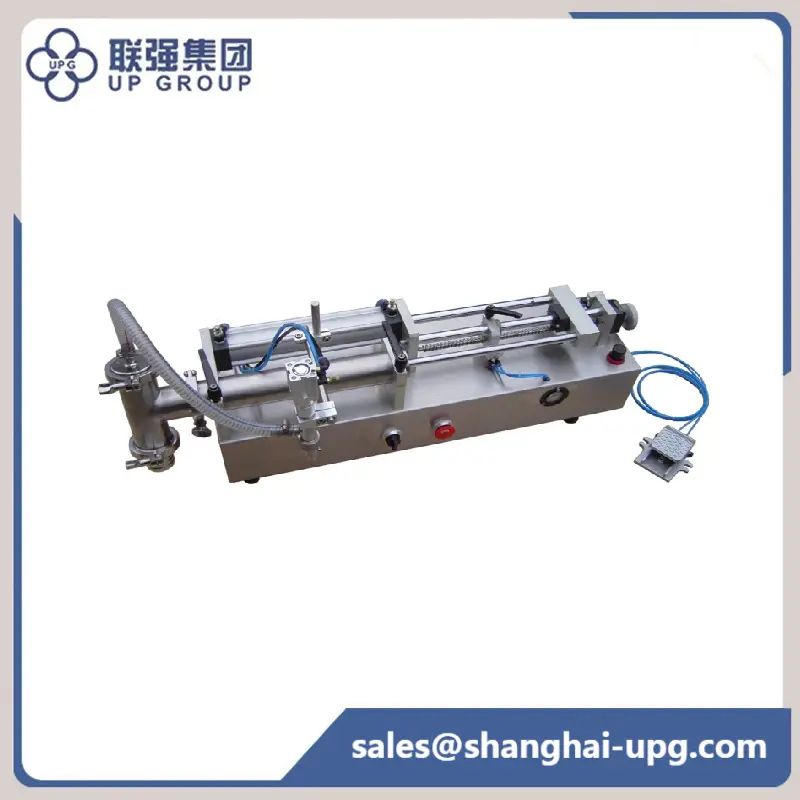
One of the main goals of a liquid filling machine is to ensure accuracy and consistency in the filling process. Inaccurate filling can lead to product waste, customer dissatisfaction and regulatory issues, especially in industries such as pharmaceutical, food and beverage. As a result, manufacturers invest in high-quality liquid filling machines that provide accurate measurements and consistent performance over time.
To ensure optimal performance, liquid filling machines must be regularly maintained and calibrated. This includes cleaning the filling nozzles, checking for leaks and calibrating the filling volume to ensure accuracy. Manufacturers should follow the recommended maintenance schedule provided by the machine's manufacturer to prevent downtime and ensure the longevity of the equipment.
Liquid filling machines are an important part of the manufacturing and packaging industry, improving the efficiency, accuracy and consistency of the filling process. By understanding the principles behind these machines, manufacturers can make informed decisions about the type of filling equipment that best suits their needs. Whether gravity, piston, vacuum or pressure filling methods are used, the goal is the same: to provide consumers with a high-quality product while optimizing productivity. As technology continues to advance, liquid filling machines will continue to evolve, offering greater levels of precision and automation to meet the demands of modern manufacturing.
Post time: Dec-16-2024