Filling machines are essential in various industries such as food and beverage, pharmaceutical, cosmetic and chemical. Among the various types of filling machines, screw-type filling machines stand out for their precision and efficiency. In this article, we will delve into the theory behind filling machines, specifically screw-type filling machines, exploring their mechanisms, applications and advantages.
The core design of a filling machine is to dispense a specific volume of liquid, powder or granular material into a container. Its primary goal is to ensure accuracy and consistency in the filling process, which is critical to maintaining product quality and meeting regulatory standards.
Filling machines can be categorized into a number of types depending on their operation and the nature of the product being filled. These include gravity fillers, pressure fillers, vacuum fillers and screw fillers. Each type has its own unique mechanism for different applications.
The principles of filling machines are centered around the following key principles:
1. Volume Measurement: It is critical to accurately measure the volume of the product. This can be achieved by a number of methods, including volumetric, gravimetric or mass flow measurement. The choice of measurement method usually depends on the characteristics of the product and the required filling accuracy.
2. Flow control: Controlling the product flow during the filling process is critical to prevent spillage or underfilling. This can be managed through a variety of mechanisms such as pumps, valves and sensors that work together to regulate the flow rate. 3.
3. Container Handling: Filling machines must be designed to accommodate containers of different shapes and sizes. This includes devices to position, stabilize and transport containers during the filling process.
4. Automation and control systems: Modern filling machines often utilize advanced automation and control systems to improve efficiency and accuracy. These systems include programmable logic controllers (PLCs), touch screens, and sensors that monitor the filling process in real time.
Check out one of our company’s products, LQ-BLG Series Semi-auto Screw Filling Machine
LG-BLG series semi-auto screw filling machine is designed according to the standards of Chinese National GMP. Filling, weighing can be finished automatically. The machine is suitable for packing powdery products such as milk powder, rice powder, white sugar, coffee, monosodium, solid beverage, dextrose, solid medicament, etc.
The filling system is driven by servo-motor which have the features of high precision, large torque, long service life and the rotation could be set as requirement.
The agitate system assemble with the reducer which is made in Taiwan and with the features of low noise, long service life, maintenance-free for all its life.
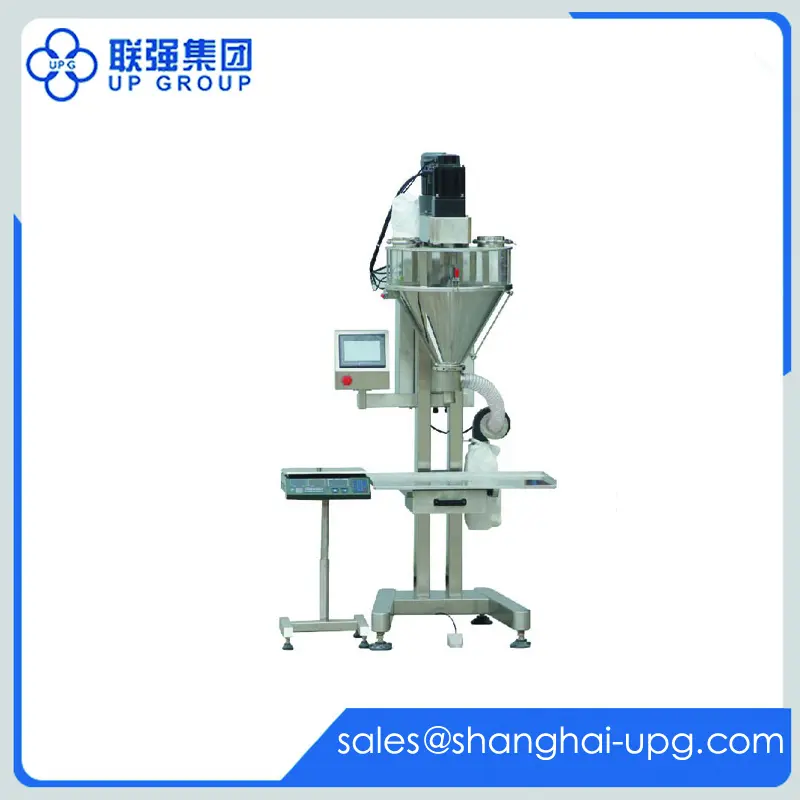
Understanding Screw Filling Machines
Screw fillers are a special type of filling machine that utilizes a screw mechanism to dispense the product. They are particularly effective for filling powders, granules and viscous liquids. The operation of a screw filler can be broken down into several key parts:
1. Screw mechanism
The screw mechanism is the heart of a screw filler. It consists of a rotating screw that conveys the product from the hopper to the filling nozzle. The screw is designed to precisely control the amount of product dispensed. As the screw rotates, it pushes the product forward and the depth of the thread determines the amount of product filled into the container.
2. Hopper and feeding system
The hopper is where the product is stored before filling. It is designed to ensure a steady flow of material to the screw unit. Depending on the characteristics of the product, the hopper may include features such as a vibrator or agitator to prevent agglomeration and ensure a steady feed.
3. Filling nozzles
The filling nozzle is where the product leaves the machine and enters the container. The design of the nozzle can vary depending on the product to be filled. For example, nozzles for filling viscous liquids may have larger openings to accommodate thicker consistencies, while nozzles for filling powders may have smaller openings to ensure accuracy.
4. Control systems
Screw filling machines are usually equipped with advanced control systems that allow the operator to set parameters such as filling volume, speed and cycle time. These systems also provide real-time feedback for quick adjustments to maintain accuracy and efficiency.
Applications of Screw Filling Machines
Screw filling machines are widely used in various industries due to their versatility and high precision. Some common applications include
- Food industry: Filling of powdered flavorings, sugar, flour and granular products.
- Pharmaceutical industry: Dispensing of powdered medicines, supplements and granules.
- Cosmetics: Filling of creams, powders and other cosmetics.
- Chemicals: Filling of industrial powders and granular materials.
Advantages of Spiral Filling Machines
Spiral filling machines offer several advantages that make them the first choice for many manufacturers:
1. High precision: The screw mechanism allows precise control of the filling volume, reducing the risk of over- or under-filling.
2. Versatility: Handles a wide range of products from powders to viscous liquids for a variety of applications.
3. High efficiency: Screw fillers can operate at high speeds, increasing productivity and reducing labor costs.
4. Automation: Many screw fillers are equipped with automation features that can be seamlessly integrated into production lines, reducing production costs.
In short, understanding the theory of filling machines, especially screw filling machines, is crucial for manufacturers looking to optimize their filling process. With their precision, efficiency and versatility, screw filling machines play a vital role in ensuring product quality across industries. As technology continues to advance, these machines are likely to become even more sophisticated, further enhancing their functionality and applications.
Post time: Oct-21-2024